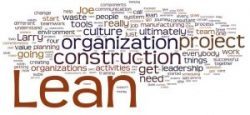
Uma experiência prática de Lean Construction
19 de setembro de 2016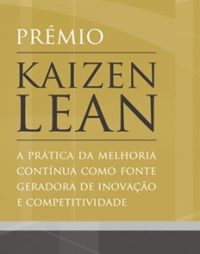
Kaizen e Lean na melhoria das empresas brasileiras hoje
19 de setembro de 2016O objetivo do projeto foi melhorar o fluxo de materiais dentro do setor de acabamento de produtos rotomoldados de uma empresa situada no interior de São Paulo. O setor em questão é caracterizado por mão-de-obra intensiva e utilização de aparelhos simples, sem tecnologia avançada. Cada operador trabalha em sua própria bancada.
O setor possuía layout funcional, que é caracterizado por subsetores dedicados a tarefas específicas. Os produtos em processamento necessitavam ser movimentados constantemente entre um subsetor e outro. Dado que estes produtos nem sempre possuem o mesmo roteiro, por não necessitarem ser trabalhados em todos os subsetores ou precisarem ser retrabalhados em uma etapa anterior, seu controle é muito complexo, o que torna difícil e ineficiente o trabalho dos estoquistas. Outro ponto negativo deste método de arranjo é a grande quantidade de trabalhos em processo, ou seja, produtos que haviam passado por algumas etapas de acabamento e estavam esperando para passar por outras. O resultado disso é a criação de muitas filas, cada uma com itens em estados diferentes.
A proposta de melhoria visou eliminar essa complexidade. O setor, que antes possuía layout funcional, passou a trabalhar em layout celular. Nessas células, os operadores fariam a inspeção das peças assim que chegassem à bancada, para eliminar eventuais refugos e decidir quais etapas eram necessárias e, após isso, realizariam essas etapas de modo sequencial. Assim, o item seria inteiramente feito e inspecionado por uma única pessoa, só havendo filas de itens para serem trabalhados antes da célula e prontos após ela, eliminando-se todas as filas intermediárias.
Figura 1 – Mudança no layout e na movimentação de produtos em processo
A figura 1 mostra a mudança no layout e no caminho percorrido pelos produtos. A figura 2 mostra a mudança com relação ao trabalho dos operadores, que passaram de especializados em uma única tarefa para multifuncionais, além de terem agregada a tarefa de inspeção de produtos.
Figura 2 – Mudança na bancada dos operadores e nas suas funções
A implementação desse projeto se deu basicamente em dois passos: medida da eficiência e de qualidade e treinamento dos operadores. No primeiro passo, foi medida a eficiência de um operador realizando as atividades separadas e, em um segundo momento, realizando todas em sequência. O resultado desse teste foi um aumento na sua eficiência de cerca de 30%, sem perda de qualidade. Uma vez provado que a mudança seria benéfica do ponto de vista da produtividade, o segundo passo visou garantir que todos os trabalhadores soubessem realizar todas as etapas de acabamento. Eles passaram a atuar em bancadas preparadas para todas as tarefas, sendo acompanhados de perto pelo líder do setor e pelo pessoal de processos, garantindo que seguissem o procedimento padrão. A princípio houve uma queda significativa na eficiência do setor, mas, após cerca de uma semana, essa eficiência havia ultrapassado a sua média histórica.Dentre os benefícios da nova disposição, destacam-se:
- Melhora no fluxo dos produtos dentro do setor;
- Diminuição do lead-time de produção;
- Melhora na eficiência do operador em cerca de 30%;
- Diminuição do custo de mão-de-obra por unidade produzida;
- Eliminação de estoque em processo dentro do setor;
- Aumento do senso de qualidade dos operadores;
- Melhora na ergonomia.
O texto acima foi escrito por Humberto Govoni, Engenheiro de Produção, que conduziu o projeto prático em questão.
O projeto foi apresentado no contexto do treinamento Lean Pro e serviu como pré-requisito para sua certificação pela Auctus como Lean Practitioner.
Tendo interesse no curso de Lean, visite nossa agenda.
Outros projetos: