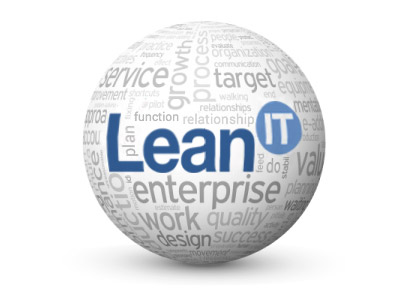
O que é Lean IT ?
19 de setembro de 2016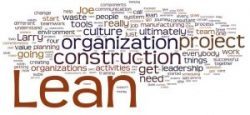
Uma experiência prática de Lean Construction
19 de setembro de 2016Com os objetivos de melhorar os processos e o dia-a-dia da gráfica, foram escolhidas as ferramentas Kanban e 5S. As ferramentas foram escolhidas e aplicadas considerando-se a dinâmica de trabalho da gráfica.
KANBAN
Inicialmente foi feito um levantamento das atividades da gráfica e verificação dos materiais que eram mais consumidos. Obteve-se que o Papel A4 e três tipos de papel em rolo para plotter eram os mais utilizados. Foi verificado problemas de controle de estoque, já que o mesmo era controlado por contagens esporádicas. Dessa forma, foi definida a aplicação de Kanban para o controle de estoque com os objetivos de facilitar controle com a gestão visual, evitando perda de material, por estoque parado, e esquecimentos de compras. Além disso, o Kanban reduziria o trabalho desnecessário de inúmeras contagens, havendo também um ganho de tempo de trabalho.
Foi aplicada a fórmula para cálculo de Kanban’s para cada material. Levando-se em conta a dinâmica das atividades da gráfica e a questão de reposições, a quantidade de Kanban’s foi readequada de acordo com o consumo semanal. Os Kanban´s foram fixados na entrada do estoque de cada material, afim de que o controle dos cartões fosse feito imediatamente ao consumo para evitar esquecimentos.
Anteriormente, eram comprados um volume grande de papéis. Além disso, quando faltava material por não realização de pedido, eram compradas caixas diretamente do comércio, com custo mais alto. Com a gestão de estoque por Kanban´s o volume comprado chega a ser 60% menor em alguns tipos, com menor chance de compras emergenciais. Com isso, passou a sobrar caixa livre para uso em necessidades imediatas que antes eram material estocado ou ainda, material inutilizado por perda de qualidade.
5S
A ferramenta 5S foi aplicada visando melhorar o ambiente de trabalho, a execução das atividades, utilização dos equipamentos e a atitude da equipe em relação aos materiais e equipamentos, ou seja, mudanças físicas, intelectuais e comportamentais.
Seguindo as etapas do 5S, primeiramente foi realizada a Seleção. Os materiais foram alocados̸ guardados conforme a frequência de utilização. Os materiais de uso contínuo, como material de plastificação e espirais, foram guardados em locais de fácil acesso e materiais pouco utilizados, como materiais para fabricação de carimbo e estampagem, foram alocados em estantes mais altas. Um grande estoque de sobras de papel foi descartado por não utilização.
Na etapa Ordenação, foi criado um Scrum para gerenciamento das atividades. Por ser uma gráfica rápida, o quadro foi dividido por horários. Além disso, as caixas de papel A4, que eram alocadas em diferentes lugares, dependendo da quantidade e disponibilidade de local, passaram a ser estocadas em um pallet, para evitar umidade e em local específico.
Na etapa limpeza, foram colocadas lixeiras próximas as plotters para sobras de papel de rolo e assim facilitar a remoção de sobras. Antes, as sobras ficavam no chão até que em algum momento que sobrasse tempo fossem recolhidas. A necessidade de buscar sacolas para a remoção dos papeis tornava a limpeza mais demorada e dessa forma, a tarefa era sempre postergada. Após a seleção dos materiais nas bancadas, as mesmas foram limpas e somente o material de uso contínuo foi deixado nestas.
Na etapa de padronização, foi definido que uma tesoura seria alocada sobre cada mesa de corte para que não fosse necessário retirá-las no local onde ficavam todas as tesouras. Muitas vezes as tesouras também eram perdidas, pois em meio aos pedidos as tesouras não eram devolvidas ao mesmo local. Posicionadas em cada mesa, já estarão sempre próximas ao local de uso, sem necessidade de busca-las, o que as vezes ocorria com a sala do segundo andar, ou procura-las, pois não haveria necessidade de utilizá-las em outro local. Os papéis de qualidade diferentes e em menores quantidades foram organizados em caixas padrão que foram etiquetadas. Anteriormente, esses materiais ficavam sobre a bancada, podendo ser danificados com a sobreposição e a exposição ao ambiente. O controle da quantidade destes materiais também era dificultado com a forma que eram armazenados. As embalagens agora estão alocadas em local de passagem, mais próximas do balcão de entregas. Dessa forma, não há a necessidade de se deslocar para o interior da gráfica somente para retirar uma embalagem e nem parar algum processo de corte.
Por fim, na etapa disciplina, foi definido que ao final de cada dia de trabalho seria realizado uma limpeza simples, somente para “manter as coisas em ordem”. Como todas as etapas já haviam sido realizadas e a gráfica limpa e organizada não serão necessários grandes esforços para manter a gráfica do mesmo modo com as organizações diárias. Dessa forma, foi obtido um ambiente de trabalho mais limpo, organizado e prático para execução das atividades.
O texto acima foi escrito por Fernanda Hara, engenheira de materiais, que conduziu o projeto prático em questão, projeto muito bem avaliado pela empresa onde foi aplicado.
O projeto foi apresentado no contexto do treinamento Lean Pro e serviu como pré-requisito para sua certificação pela Auctus como Lean Practioner.